A meat manufacturer wanted to redesign and automate their production process entirely. The meat manufacturing process involves many complicated steps such as managing the incoming raw materials, inventory management, full product traceability, and planning and scheduling orders. Automation would simplify the complexity, giving them a paperless environment with significantly reduced human error
A Real Solution Requires Real Understanding
Nowadays, consumers want to know the origin of the animal before buying the product off the counter. Therefore, meat traceability is essential as it establishes trust in the quality and safety of the product. Ensuring transparency at every stage is also one of the key factors in minimising food contamination risks, fulfilling regulatory compliance requirements.
To achieve this traceability, the client needed seamless integration between the hardware and software within the factory. The client asked us to design and implement the meat processing automation solution that would achieve this. They were attracted by our vast experience in system integration, industrial connectivity, digital quality, and manufacturing IT within the Food and Beverage industry.
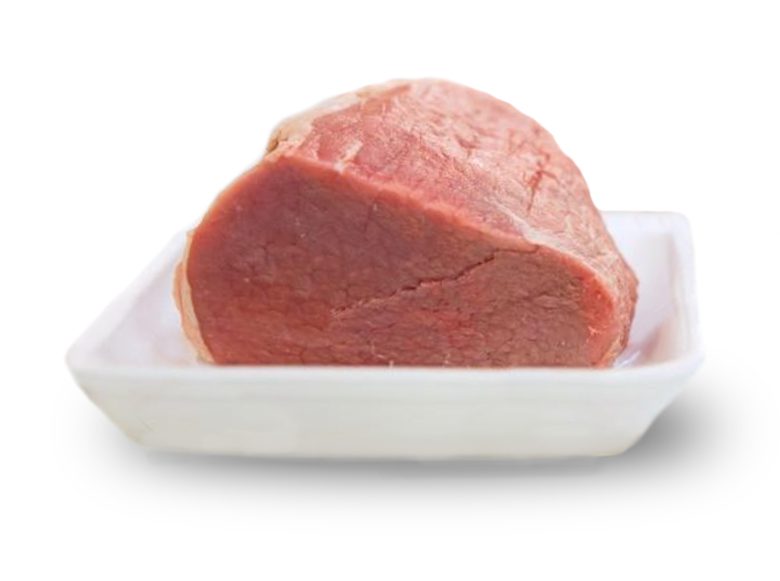

The Solution Approach
Our consultants and engineers have a wealth of experience in automation & IT, Lean & Six Sigma, Quality Management, and Product Lifecycle Management (PLM), which gives them unique insights into the challenges and potential solutions presented. They analysed the existing system thoroughly, aided by BPMN (Business Process Model Design). This would help map every action, reaction, and interaction throughout the meat production process.
ATS MeatIT was selected as an ideal fit for the project. As a Manufacturing Execution System / Manufacturing Operations Management (MES/MOM) solution ATS MeatIT provides flawless manufacturing processes by providing a single source for your data and enabling real-time updates when requirements change.
The ATS team created a simulation of the planned meat processing line to identify hurdles and eliminate them before bringing them to the real world. Then, they designed a well-prioritised project to arrive at the solution while considering all elements such as people, process, and technology.
The Results
The solution addressed data silos by integrating the factory floor hardware and their existing ERP (Enterprise Resource Planning) system. Through this, they attained a greater ability to monitor production and, as a result, were able to raise OEE (Overall Equipment Effectiveness).
With the help of RFID tags and scanners, individual products could be tracked and traced throughout the process. In addition, they greatly improved planning and scheduling capabilities and could monitor inventory in real-time.
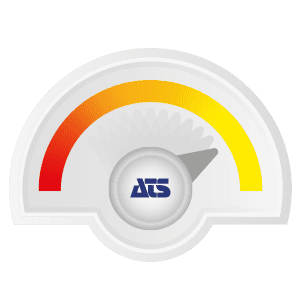